Paint rollers are one of the most commonly used tools in painting. They are designed to help painters to cover large areas with paint quickly and efficiently.

Paint rollers are made from various materials, including foam, microfiber, and wool. They are attached to a handle made from plastic or metal. In this article, we will explore the manufacturing process of paint rollers in detail.

The manufacturing process of paint rollers involves several steps. These steps include selecting materials, preparing materials, cutting and trimming, rolling, and packaging. Let’s explore each step in more detail about paint roller manufacture.
Selection of Materials

The first step in the manufacturing process of paint rollers is the selection of materials. Different materials can be used to make paint rollers, including wool, synthetic materials, foam, and microfiber. The choice of materials depends on the type of paint and the surface being painted.
Wool is the most traditional material used to make paint rollers. It is made from the fleece of sheep and is known for its durability and ability to hold large amounts of paint. Synthetic materials such as polyester and nylon are commonly used to make paint rollers. They are more affordable than wool and are easy to clean.
Foam rollers are made from a foam material typically used for painting smooth surfaces such as walls and ceilings. Microfiber rollers are made from a polyester and nylon blend and are ideal for painting rough surfaces such as stucco or brick.
Preparation of Materials
After selecting the materials, they must be prepared for the manufacturing process. This includes cleaning and cutting the materials to the correct size.
Wool fibres are cleaned to remove dirt and other impurities. They are then carded, which involves separating and straightening the fibres. This process prepares the wool fibres for spinning.
Synthetic materials are melted and extruded through a spinneret to create a continuous filament. The filament is then cut into short fibres that can be used to make the paint roller.
The foam material is cut into strips of the correct size for the paint roller.
Cutting and Trimming
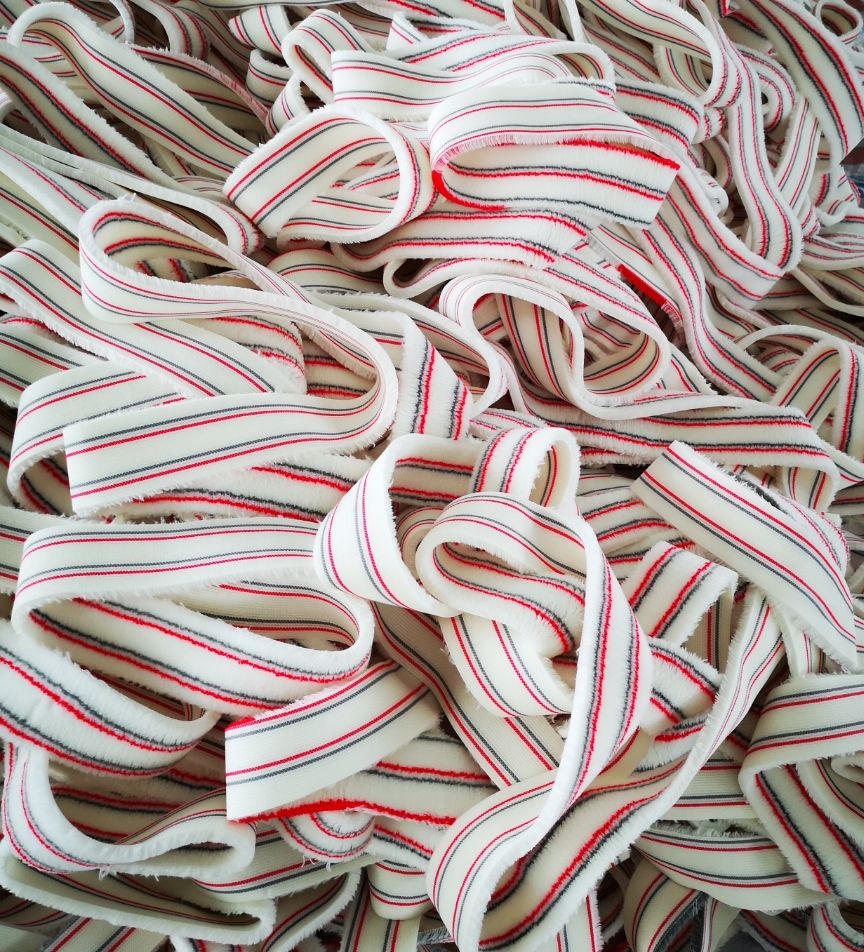
After the materials have been prepared, they are cut and trimmed to the correct size and shape. This involves cutting the materials to the appropriate length and width and trimming any excess material.
Wool fibres are spun into yarn and wound onto a spindle. The yarn is then cut to the appropriate length and attached to the roller handle.
Synthetic fibres are cut to the appropriate length and attached to the roller handle using an adhesive.
Foam strips are cut to the appropriate width and length and attached to the roller handle.
Rolling

The rolling process involves attaching the roller to the handle and shaping the roller to the correct shape. This is done using a rolling machine that compresses the material and shapes it into the desired shape.
Wool rollers are rolled into a cylindrical shape and compressed to create a dense roller. The roller is then attached to the handle using a metal frame.
Synthetic rollers are rolled into a cylindrical shape and compressed to create a dense roller. The roller is then attached to the handle using an adhesive.

Foam rollers are rolled into a cylindrical shape and compressed to create a dense roller. The roller is then attached to the handle using an adhesive.
Packaging

The final step in the manufacturing process of paint rollers is the packaging. The rollers are packaged in boxes or plastic wrap and shipped to retailers.
Conclusion
Paint rollers are a vital tool in the painting industry. They are used to cover large areas quickly and efficiently. The manufacturing process of paint rollers involves several steps, including selecting materials, preparing materials, cutting and trimming, rolling, and packaging. Different materials can be used to make paint rollers, including wool, synthetic materials, foam, and microfiber. Each material has its unique advantages and disadvantages. Wool is known for its durability and ability to hold large amounts of paint, but it can be more expensive than synthetic materials. Synthetic materials are more affordable and easy to clean but may not hold as much paint as wool. Foam rollers are ideal for painting smooth surfaces but may not be as durable as wool or synthetic materials. Microfiber rollers are ideal for painting rough surfaces but may not be as widely available as other materials.
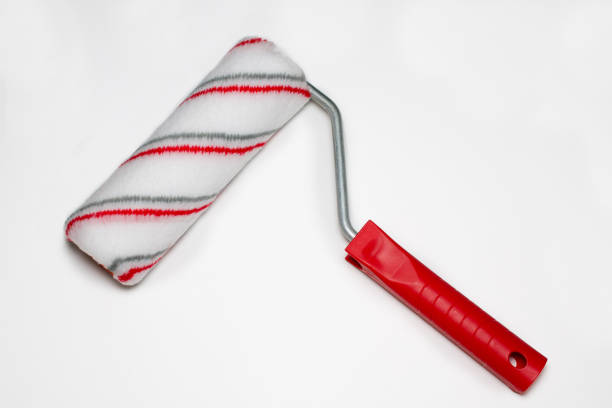
In conclusion, the manufacturing process of paint rollers involves carefully selecting materials, preparing those materials, cutting and trimming, rolling, and packaging. Each step is essential to creating a high-quality paint roller that will perform well and last long. By understanding the manufacturing process of paint rollers, we can appreciate the hard work of creating a simple yet essential tool for the painting industry.

Moreover, the manufacturing process of paint rollers is not just about creating a functional tool but also about ensuring that the tool is safe and eco-friendly. Many manufacturers use sustainable materials and eco-friendly manufacturing processes to reduce their environmental impact. For example, some manufacturers use recycled materials, such as recycled polyester, to create synthetic paint roller covers. Others use natural or organic materials, such as organic wool, to create paint rollers free from harmful chemicals and toxins.
In addition to materials, the manufacturing process ensures that the paint roller is safe for use. This includes testing the roller for quality and safety standards. For example, some paint rollers may be tested for durability by simulating repeated use over a certain period. Other rollers may be tested for safety by checking for sharp edges or other hazards.
Overall, the manufacturing process of paint rollers is a complex and vital process that involves careful consideration of materials, safety, and eco-friendliness. By understanding the manufacturing process, we can better appreciate the value of this simple yet essential tool in the painting industry. Whether we are DIY painters or professional contractors, a high-quality paint roller can make all the difference in achieving a flawless finish.

Get Good Quality Paint Rollers from Paintbrusha
Looking for high-quality paint rollers? Look no further than Paintbrusha. Paintbrusha is a leading supplier of premium-quality paint rollers, offering a wide range of products to meet the needs of both professional and DIY painters.
Paintbrusha’s paint rollers are made from high-quality materials, ensuring they are durable, long-lasting, and capable of delivering consistent results. The rollers are available in various sizes and textures, so you can choose the one that best suits your needs. Whether you are painting a smooth surface or a textured one, Paintbrusha has the perfect roller for you.

In addition to offering high-quality rollers, Paintbrusha also provides exceptional customer service. Our team is knowledgeable and experienced, ready to answer any questions you may have about our products or painting in general. We also offer fast and reliable shipping, so you can receive your rollers quickly and start painting immediately.
One of the advantages of using Paintbrusha’s rollers is that we are compatible with various paint types, including latex, oil, and acrylic. This versatility means using the identical roller for multiple projects, saving time and money.
Another advantage of using Paintbrusha’s rollers is that they are easy to clean and maintain. After use, rinse the roller with warm water and soap, and it will be ready for the next project. This ease of maintenance makes Paintbrusha’s rollers an excellent investment for professional and DIY painters.
In conclusion, selecting the right paint roller is critical to achieving a high-quality finish when painting. Paintbrusha’s rollers are excellent for high-quality, versatile, and easy-to-use rollers. With their exceptional customer service and fast shipping, Paintbrusha is the go-to destination for all your painting needs.
